在现代制瓶过程中除了要用压缩空气对玻璃料滴进行倒气正吹气等吹制工序,其模具还必须适时地排除其模腔空间(Voids)里所占有的气体,让出空间使得玻璃液迅速贴紧模腔,生产出合格的玻璃瓶。
一、模具排气历史的回顾:
一、模具排气历史的回顾:
早在1882年亚博加斯特(Arbogost)在美国发明了压&吹法(Press&Blow Process),在同时代1885年英国的阿什累(Ashley)发明了用吹&吹工艺(Blow&Blow)来制造玻璃瓶。在此二个制瓶工艺发明之前。制瓶完全处在手工操作的阶段,制瓶人对模具的排气也没有概念,制瓶的速度也全在于制瓶师傅们“手中的活”。如果玻璃瓶出现由于排气的缺陷,师傅们手中可以慢一点使得模具从容地排出气体。但经过多年的实践与总结,当时的制瓶人也逐步认识到模具排气在制瓶过程中的必要性与重要性。因此在手工操作的模具排气上也开始受到重视并做了大量的工作。
下图一的专利就是关于模具排气当年的例子之一。
下图一的专利就是关于模具排气当年的例子之一。
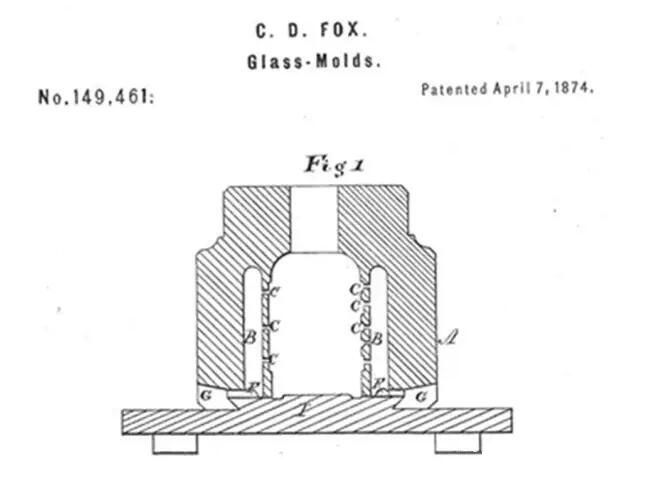
图一 1874年4月7日模腔排气的专利,专利号:149461
此专利距今天已有143年,从此专利图中我们可以看到其成模上、中、下均有排气孔C,然后与大孔B钻通由G孔排出成模。可见当年还在手工操作时的情况下,我们同行前辈们就已经认识到模具排气的重要性,它排气原理与今天的排气基本相似。
二、现代制瓶模具排气问题的提出及解决方法:
现代随着制瓶高速化以及轻量化的发展,玻璃瓶模具加工的精度也随之提高。现在模具的合缝线等配合精度已经做到了可谓严丝合缝密不透风,其模具的腔室(Cavity)几乎是密闭的。而人们对玻璃瓶的质量要求越来越高,因此在现代制瓶过程中模具排气的问题日趋凸出。人们不仅在成模处打了排气孔,还在其他模具中也采取了不同的排气措施,那么模具在现代制瓶生产吹&吹法过程中到底有几处需要排气的?
1. 初模侧
根据落料的需要:当料滴以自由落体的速度落进初模模腔里,其模腔是合拢关闭腔室也是密闭的(Voids),其下部的气体必须要排出让位于料滴的进入。初模侧模具的排气包括有:
⑴ 芯子的排气(Vent)
芯子上开一类似S的槽并且打一小穿孔以排除其气体,见图二。
二、现代制瓶模具排气问题的提出及解决方法:
现代随着制瓶高速化以及轻量化的发展,玻璃瓶模具加工的精度也随之提高。现在模具的合缝线等配合精度已经做到了可谓严丝合缝密不透风,其模具的腔室(Cavity)几乎是密闭的。而人们对玻璃瓶的质量要求越来越高,因此在现代制瓶过程中模具排气的问题日趋凸出。人们不仅在成模处打了排气孔,还在其他模具中也采取了不同的排气措施,那么模具在现代制瓶生产吹&吹法过程中到底有几处需要排气的?
1. 初模侧
根据落料的需要:当料滴以自由落体的速度落进初模模腔里,其模腔是合拢关闭腔室也是密闭的(Voids),其下部的气体必须要排出让位于料滴的进入。初模侧模具的排气包括有:
⑴ 芯子的排气(Vent)
芯子上开一类似S的槽并且打一小穿孔以排除其气体,见图二。
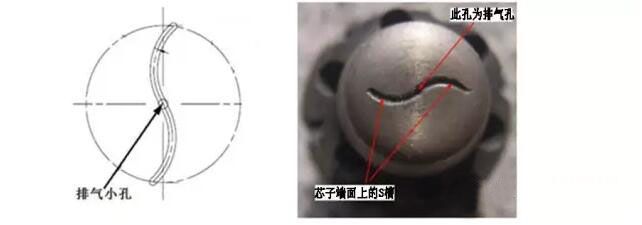
图二 芯子S槽的排气
在芯子中心钻一通孔孔径0.3-0.5毫米左右不等,沿着此孔在芯子的表面加工一S型的槽沟,在落料时此S排气槽可以帮助口模下方密闭空间将气体排出,使得料滴下落时料滴快速进入口模与芯子处。
在生产一些细长颈的玻璃瓶或者其他特殊的玻璃瓶时,为了加速排气有人在芯子上加工三道S槽的。见图三左:更有人设计芯子由二体组成,由一芯棒压紧在芯子里,芯棒上端与芯子有间隙,此间隙与下段的一侧孔相通然后再与直孔接通用于排气。由于此间隙是一圈的,因此其排气效果大大优于S槽,见图三右。
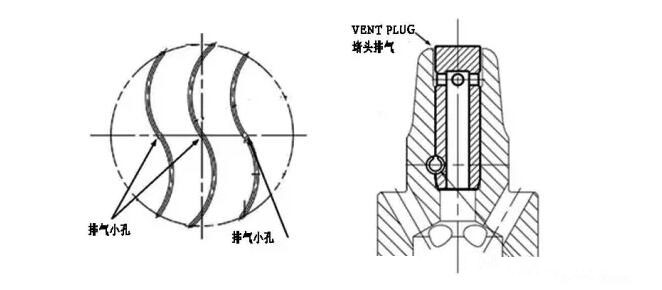
图三 三条S槽及二段式芯子的排气
⑵ 口模的排气(Vent)
口模在与初模配合处设有排气槽,见图四。
口模在与初模配合处设有排气槽,见图四。
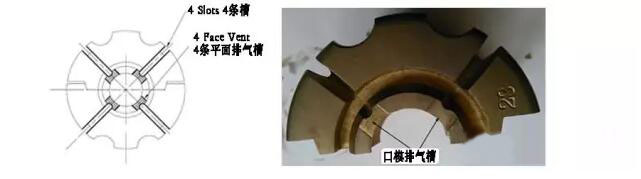
图四 口模排气的图示
从图四可以看到口模与初模接合处有四条排气槽,其宽度10-14毫米深0.05-0.08毫米不等。此排气槽经初模燕尾槽上的排气孔排出模腔外部见图五:
⑶ 初模的排气(Vent)
初模下段处也设有排气槽,见图五。
⑶ 初模的排气(Vent)
初模下段处也设有排气槽,见图五。
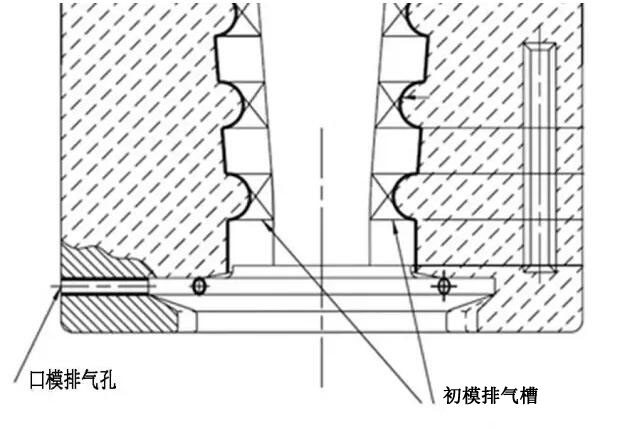
图五 初模排气槽的图示
初模的排气槽有三条其宽度和深度与口模相似。由于初模有三道排气槽当料滴落下进入模腔后它的排气效果是较大的。
初模侧这三个模具的排气(Vent)均为了落料快速顺畅地进入初模的低端,料滴可迅速在口模与芯子处就位。有制瓶专家曾说落料的顺畅它是制瓶成功的一半,这话说得中肯。在生产长、细颈玻璃瓶时为了保证落料顺畅,有在初模处加装有真空以辅助落料迅速到位,这样它可以减少扑气的时间与扑气的压力,减轻扑气箍(Settle Wave),进而提高玻璃液的均匀分布。
近几年,由于真空新技术的发展,一种由压缩空气冲出以射流附壁原理而产生真空应用与玻璃瓶行业。用此真空辅助落料它称为LPBB(Light Production Blow&Blow Process)的制瓶工艺(又称9.5法)。LPBB法是初模采用真空形成瓶口的工艺法,其原理见图六。
初模侧这三个模具的排气(Vent)均为了落料快速顺畅地进入初模的低端,料滴可迅速在口模与芯子处就位。有制瓶专家曾说落料的顺畅它是制瓶成功的一半,这话说得中肯。在生产长、细颈玻璃瓶时为了保证落料顺畅,有在初模处加装有真空以辅助落料迅速到位,这样它可以减少扑气的时间与扑气的压力,减轻扑气箍(Settle Wave),进而提高玻璃液的均匀分布。
近几年,由于真空新技术的发展,一种由压缩空气冲出以射流附壁原理而产生真空应用与玻璃瓶行业。用此真空辅助落料它称为LPBB(Light Production Blow&Blow Process)的制瓶工艺(又称9.5法)。LPBB法是初模采用真空形成瓶口的工艺法,其原理见图六。
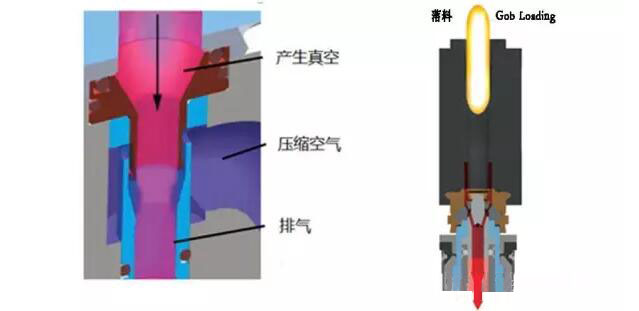
图六 LPBB工艺初模侧真空原理图
此种真空的产生仅用压缩空气作动力,不需要另外的真空泵与管路设备简单可靠。由于此种制瓶工艺基本没有扑气,因此它少有“断腰”现象。因此可以减轻瓶重提高机速。此技术是近十几年的新发明,也是一种排气的新形式,由此派生出一种制瓶的新工艺。国外有成熟的经验,有志者可探讨一下。
(4)倒气工序的排气:
闷头的排气(Vent),在闷头的端面设有排气槽,见图七。
(4)倒气工序的排气:
闷头的排气(Vent),在闷头的端面设有排气槽,见图七。
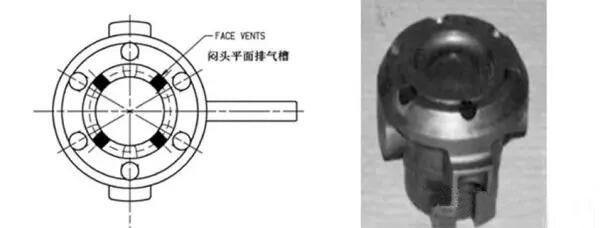
图七 闷头排气槽的图示
玻璃料团在初模中经扑气等形成瓶口与泡穴,瓶口成形后下一步是倒气。此时闷头已经就位压在初模上,它与初模配合在初模腔室上部形成一封闭的空间。要使得料胚在倒气(counterblow)的作用下迅速上升到位,此密闭空间(Void)必须要排出此处的气体,否则料胚上升时会受到阻力。因此我们在闷头端面处开有此排气槽。见图六:此排气平面槽为4-6条宽和其深度与口模相仿。因此我们用压缩空气(倒气)推动玻璃料团向初模上腔,此时闷头排气槽排出气体(Air)。料滴团迅速形成内部有空泡的初模料胚(a Bubble in the Parison)。
2.成模侧:成模的排气(Exhaust)
(1) 成模模壁处的排气孔,见图八。
2.成模侧:成模的排气(Exhaust)
(1) 成模模壁处的排气孔,见图八。
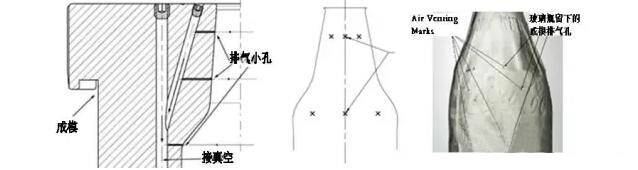
图八 成模排气的图示
从初模翻转进入成模,成模的模腔比料胚大的多,在正吹气的作用下料胚会迅速被吹涨,此时成模模腔四周“埋伏(Air Trapped)”着的气体要迅速排出。一般在成模的瓶身与瓶颈处钻几排的排气孔(如图八就有三排排气孔)。小排气孔钻接通垂直的大孔而大孔与真空管孔相连用真空辅助帮助排气,它排气原理与图一1874年专利基本相同。这样在正吹气、排气孔与真空(Final Blow,Exhaust,Vacuum)三管齐下,可将初模料胚迅速吹制成玻璃瓶的形状。此处真空是自然排气的重要补充,是强制排气的一种形式。
(2) 成模底部的排气(Vent)
有些玻璃瓶比如方瓶、长方形瓶以及多角瓶的玻璃瓶它对瓶底的四角要求很高。此类玻璃瓶在正吹气时常会发生瓶底打不足或者瓶底四角不挺等现象。玻璃瓶在正吹气时其吹制过程如图九。
(2) 成模底部的排气(Vent)
有些玻璃瓶比如方瓶、长方形瓶以及多角瓶的玻璃瓶它对瓶底的四角要求很高。此类玻璃瓶在正吹气时常会发生瓶底打不足或者瓶底四角不挺等现象。玻璃瓶在正吹气时其吹制过程如图九。
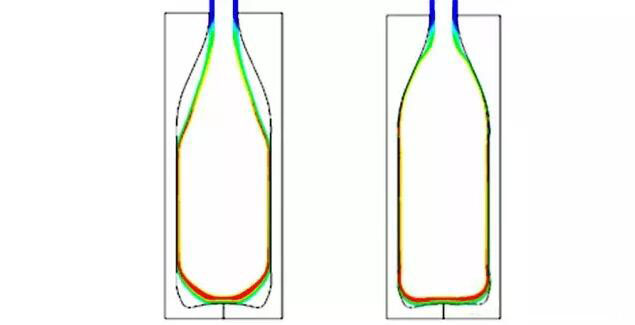
图九 瓶底四角是最后成形
因为玻璃瓶在正吹气吹制时,瓶底四角的成形是较后的,因此在这类玻璃瓶瓶底四角也要打排气孔,如图十。
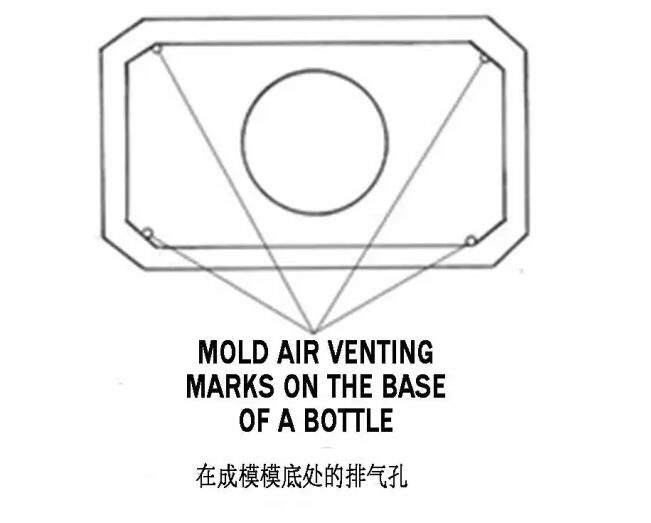
图十 模底排气图示
经过瓶底排气,多角的玻璃瓶瓶底均能达到瓶底各角饱满挺括,能符合客户审美的要求。
(3) 吹气头的排气(Exhaust)
热玻璃瓶在吹气头作用下的内部冷却排气(Exhaust),见图十一。
(3) 吹气头的排气(Exhaust)
热玻璃瓶在吹气头作用下的内部冷却排气(Exhaust),见图十一。
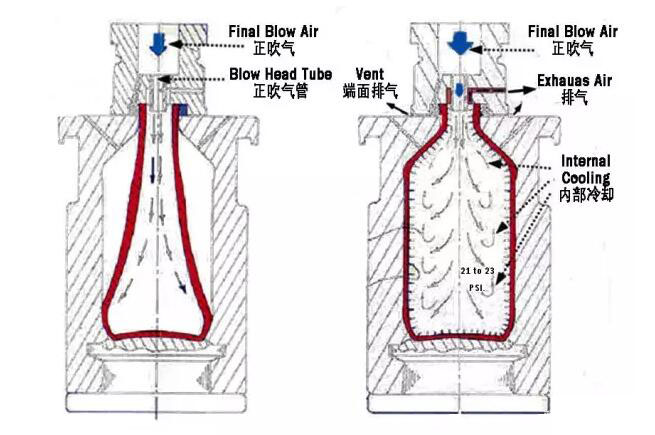
图十一 吹气头多路的排气
从图十一中可见当料胚吹涨后玻璃紧贴成模模壁,此时玻璃外表面已冷却下来,而热瓶的内部却得不到充分的冷却,热瓶内部高温不减。形成了所谓“外焦里嫩”现象。根据Emhart公司调查研究成模处散热情况为:成模散热占42%(Transferred to mold),瓶底散热占16%(Bottom Plate),正吹气散热占22%(During Final Blow),对流散热占13%(convective),正吹气内部冷却散热占7%(Internal Cooling)。此时正吹气要继续吹气欲将热玻璃瓶7%的内部热量快速排出。正吹气通过吹气管源源不断向热瓶里吹冷气,而瓶内的热气体通过气头不断地向外排出如此循环不断,终将成模侧的热瓶7%的内部热量排出。在此吹气头的热瓶内部冷却排气其效果功不可抹(InternalCooling)。
(4)吹气头端面的排气(Vent)
在吹气头压在成模的端面处也设有几道排气槽(Vent),它的作用是防止成模瓶口处的气压过高,可避免造成瓶口变形等缺陷。见图十一右:由于此排气槽不与玻璃液接触不会有玻璃液渗出之忧,因此它的深度根据不同工况可适当深些。
综上所叙,吹&吹法在制瓶生产中模具的排气初模侧有四处,成模侧也是四处。不知是否包括了吹&吹法全部排气望同仁们指正。
要注意的是各工厂在设计选用模具排气时均要根据本厂制瓶机的具体情况,特别是产品的情况比如:玻璃瓶的大小、形状以及瓶颈与瓶身是否有文字、字母、图案、花纹和商标等。并要参考制瓶工艺的其他参数,选择模具的排气以优化自己的设计。
三、排气不畅造成的缺陷:
由于在制瓶生产过程中情况复杂,不可避免地会发生模具排气不良、不畅甚至堵塞等情况。因此会造成众多的缺陷,现举几例说明:
1. 瓶口毛糙(毛口)(DIRTY FINIS);
产生原因:由于初模排气不畅,落料不顺导致涂油过多过密。
2. a. 口不足(NOT MADE UP FINISH),
b.螺纹不足(NOT MADE UP THREAD),
c.瓶口凸环不足(球环不足)(notmade up bead);
产生原因:由于初模排气不畅,落料不顺未能及时到位或者由此造成的料滴在初模内跳动等。
3. a. 瓶颈吹不足(扁颈)(NOT BLOWN UPNECK),
b. 歪颈(BENT NECK);
产生原因:成模内部冷却排气不畅,造成热量未大量排出使得瓶过热,热瓶易变形;
4. a. 瓶身凹陷(瘪身)(DENTED SIDE),
b. 瓶身未吹涨(not blown up body),
c.瓶肩吹不足(塌肩)(not blown up shoulder),
d.合缝凹陷(sunkenseam),
e.垂直度不合格(歪身)(LEANER),
f.瓶身凹陷(凹身)(SUNKEN PANEL);
产生原因:成模排气小孔堵塞或者真空管堵畅,造成热瓶未能贴紧成模壁。
5. 刻字(花纹)不清(WASHED OUTENGRAVING),见图十二。
(4)吹气头端面的排气(Vent)
在吹气头压在成模的端面处也设有几道排气槽(Vent),它的作用是防止成模瓶口处的气压过高,可避免造成瓶口变形等缺陷。见图十一右:由于此排气槽不与玻璃液接触不会有玻璃液渗出之忧,因此它的深度根据不同工况可适当深些。
综上所叙,吹&吹法在制瓶生产中模具的排气初模侧有四处,成模侧也是四处。不知是否包括了吹&吹法全部排气望同仁们指正。
要注意的是各工厂在设计选用模具排气时均要根据本厂制瓶机的具体情况,特别是产品的情况比如:玻璃瓶的大小、形状以及瓶颈与瓶身是否有文字、字母、图案、花纹和商标等。并要参考制瓶工艺的其他参数,选择模具的排气以优化自己的设计。
三、排气不畅造成的缺陷:
由于在制瓶生产过程中情况复杂,不可避免地会发生模具排气不良、不畅甚至堵塞等情况。因此会造成众多的缺陷,现举几例说明:
1. 瓶口毛糙(毛口)(DIRTY FINIS);
产生原因:由于初模排气不畅,落料不顺导致涂油过多过密。
2. a. 口不足(NOT MADE UP FINISH),
b.螺纹不足(NOT MADE UP THREAD),
c.瓶口凸环不足(球环不足)(notmade up bead);
产生原因:由于初模排气不畅,落料不顺未能及时到位或者由此造成的料滴在初模内跳动等。
3. a. 瓶颈吹不足(扁颈)(NOT BLOWN UPNECK),
b. 歪颈(BENT NECK);
产生原因:成模内部冷却排气不畅,造成热量未大量排出使得瓶过热,热瓶易变形;
4. a. 瓶身凹陷(瘪身)(DENTED SIDE),
b. 瓶身未吹涨(not blown up body),
c.瓶肩吹不足(塌肩)(not blown up shoulder),
d.合缝凹陷(sunkenseam),
e.垂直度不合格(歪身)(LEANER),
f.瓶身凹陷(凹身)(SUNKEN PANEL);
产生原因:成模排气小孔堵塞或者真空管堵畅,造成热瓶未能贴紧成模壁。
5. 刻字(花纹)不清(WASHED OUTENGRAVING),见图十二。
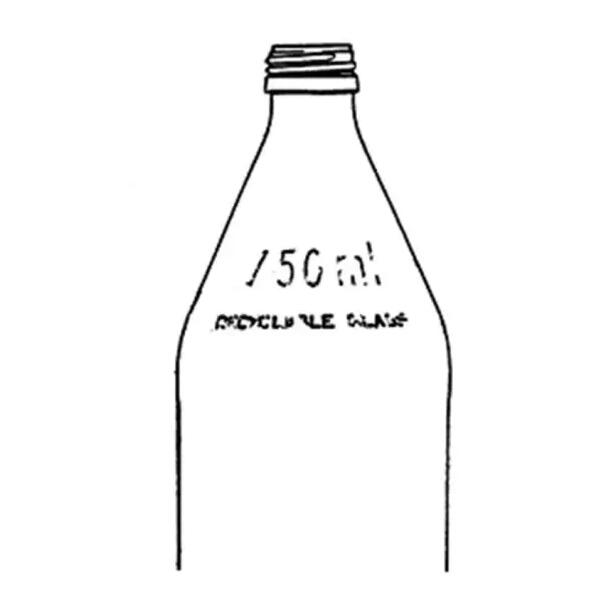
图十二 刻字(花纹)不清
产生原因:成模某排气小孔堵塞,造成此处无排气以致热瓶未能紧贴成模壁。推而广之玻璃瓶上的商标Logo、图案与字母等不清晰、模糊与不饱满等均为此原因所致。笔者曾有此几次经历。
6. 蕾丝不清(WASHED OUT B.S. STIPPLE);
产生原因:模底排气不良等原因。
由于模具排气的不畅会造成其他众多的缺陷,此处不作更详的叙说。
四、模具排气在制瓶生产中的注意点:
1. 排气平槽它包括:芯子的S槽、口模平槽、初模的平槽、闷头上的平槽以及吹气头端面的平槽,其深度一般在005-0.08毫米,仅相当于一根头发丝,在验收新模具时要特别注意测量其加工的深度与宽度,在模具车间返修时更要注意此槽的情况,是否被油灰覆盖等情况以便进行适当的再加工。
2. 排气孔它包括:成模的排气孔、模底、芯子的排气孔等。孔径仅为0.3-0.7毫米左右非常容易被热碎玻璃渣堵塞。在模具车间返修时要特别注意观察此小孔通畅与堵塞的情况,及时清除修理。
3. 由于吹气头的特殊性,在修理疏通完工后,最好用专用设备对其进气与排气的情况进行校验。
4. 在初、成模涂油时会产生大量的烟气,此烟气它对模具排气会产生很大的阻力,将会产生各种的缺陷。在现代制瓶涂油后一般要剔除3-4个热瓶(手动或者自动)。
5. 真空是自然排气的重要补充,是强制排气的一种形式。其作用不可小视。初模侧如采用真空辅助其口部成形只需6-9゜,而没有真空辅助口部成形需要35-40゜。成模的真空能使初胚瞬间贴住成模模壁快速地成形。但要注意:真空很容易吸进玻璃渣等杂物造成真空排气不畅等,对其真空设备与管路要定期清洗与维修。
6. 制瓶是一个系统整体的工作。模具的排气要与制瓶的各项参数和制瓶操作等紧密结合。比如:在成模正吹气时其内部冷却排气量的大小要根据产品的大小与机速等情况,适当调节排气盘上的孔径使冷却排气量达到最佳。
总之在吹&吹法制瓶过程中,模具的排气它关系到模具设计、模具维修、涂油润滑、电子配时等一系列的制瓶事项。以上仅是个人的见解欢迎同仁们指正与交流。
6. 蕾丝不清(WASHED OUT B.S. STIPPLE);
产生原因:模底排气不良等原因。
由于模具排气的不畅会造成其他众多的缺陷,此处不作更详的叙说。
四、模具排气在制瓶生产中的注意点:
1. 排气平槽它包括:芯子的S槽、口模平槽、初模的平槽、闷头上的平槽以及吹气头端面的平槽,其深度一般在005-0.08毫米,仅相当于一根头发丝,在验收新模具时要特别注意测量其加工的深度与宽度,在模具车间返修时更要注意此槽的情况,是否被油灰覆盖等情况以便进行适当的再加工。
2. 排气孔它包括:成模的排气孔、模底、芯子的排气孔等。孔径仅为0.3-0.7毫米左右非常容易被热碎玻璃渣堵塞。在模具车间返修时要特别注意观察此小孔通畅与堵塞的情况,及时清除修理。
3. 由于吹气头的特殊性,在修理疏通完工后,最好用专用设备对其进气与排气的情况进行校验。
4. 在初、成模涂油时会产生大量的烟气,此烟气它对模具排气会产生很大的阻力,将会产生各种的缺陷。在现代制瓶涂油后一般要剔除3-4个热瓶(手动或者自动)。
5. 真空是自然排气的重要补充,是强制排气的一种形式。其作用不可小视。初模侧如采用真空辅助其口部成形只需6-9゜,而没有真空辅助口部成形需要35-40゜。成模的真空能使初胚瞬间贴住成模模壁快速地成形。但要注意:真空很容易吸进玻璃渣等杂物造成真空排气不畅等,对其真空设备与管路要定期清洗与维修。
6. 制瓶是一个系统整体的工作。模具的排气要与制瓶的各项参数和制瓶操作等紧密结合。比如:在成模正吹气时其内部冷却排气量的大小要根据产品的大小与机速等情况,适当调节排气盘上的孔径使冷却排气量达到最佳。
总之在吹&吹法制瓶过程中,模具的排气它关系到模具设计、模具维修、涂油润滑、电子配时等一系列的制瓶事项。以上仅是个人的见解欢迎同仁们指正与交流。