解决玻璃瓶和玻璃器皿等玻璃产品条纹的有效装置
气泡、条纹、结石是玻璃制品生产过程中,容易产生的三大缺陷。特别是条纹,由于其来源较多,条纹的分析、鉴别一般工厂没有相应的设备及人才,因而解决难度大。在高档玻璃制品的生产过程中,就因为产品上痕量的条纹,致使产品不合格,造成大量的人力、物力的浪费,,严重制约生产的发展。我公司结合国内外经验以及我们近四十年在玻璃工厂工作的体会;并消化、吸收国外的先进窑炉技术及窑炉结构,就这种在玻璃制品上通过传统搅拌方法解决不了的条纹,推出供料道泄料装置,它能有效解决产品上的条纹。
下面就这种条纹产生的原因及解决原理说明如下:现在窑炉寿命要求越来越长,首先在窑炉的设计选材上,与玻璃液接触的耐火材料一般都以电熔锆刚玉砖为主,其次为了使供料道的寿命与窑炉配套,大都采用电熔锆刚玉砖做供料道的料槽砖。
我们知道,现在许多电熔锆刚玉砖生产厂家,生产电熔锆刚玉砖所用模型,是用石英砂加水玻璃作粘接剂固化成型的。石英砂的主要成份是二氧化硅Si02,纯二氧化硅Si02晶体的熔点为1725℃[1],模型使用的石英砂含二氧化硅Si02在98%左右,那么它的熔点低于1725℃,加上水玻璃(硅酸钠)混合在石英砂中,形成低共熔点,那么生产电熔锆刚玉砖砂型的熔化温度大大低于1725℃。生产电熔锆刚玉砖时,熔融AZS液体(暂且叫钢水,)成型浇铸的温度(用远红外测温仪测得的温度),33#电熔锆刚玉砖钢水的温度约为1740℃,36#电熔锆刚玉砖钢水的温度约为1760℃,41#电熔锆刚玉砖钢水的温度约为1780℃,那么在浇铸的过程中,与钢水接触的砂型有少量熔融在电熔锆刚玉砖表面。这一层所形成的晶型与内部的晶型不一样,抗侵蚀性能要差得多。生产高档玻璃时,工作池与供料道的电熔锆刚玉砖与玻璃液的接触面,最好应该加工研磨掉这层变质层,这样投产初期产生条纹的机率就小得多。
电熔熔铸耐火材料与烧结耐火材料不一样,烧结耐火材料是捣打成型,其表面的致密度要比中间的致密度高得多,在烧结过程中,砖体表面温度比中间温度高,其硅酸盐反应(瓷化或晶化反应)要比中间进行得更加完全彻底,因而烧结材料砖体表面抗侵蚀等性能要比中间好得多,所以烧结材料最好是保护其表面的完整性。而电熔熔铸耐火材料在浇铸成型的过程中,表面温度比中间融体冷却快得多,它不利于晶体的形成和生长,因而它抗侵蚀性最好部分是在中间部份。
由于槽型供料道内表面加工比较困难,国内许多电熔锆刚玉砖生产,一家还没有专门的加工设备,因此电熔锆刚玉料槽砖内表面这层抗侵蚀性能比较差的表面没有研磨掉,加上内表面不平整,接触面增大,因而侵蚀也加大。虽然供料道温度较低,侵蚀较轻微,但是这层变质层跟基础玻璃比较其氧化铝、氧化锆的含量很高,它们的融体粘度及表面张力很大,而且在供料道停留时间又短、玻璃液温度较低,腐蚀熔融物扩散不开,它顺着供料道的壁(主要是底部)流动。其次,这些变质层玻璃密度大于正常玻璃密度,容易在玻璃液流动过程中沉积于料道底部。一旦这层含氧化铝、氧化锆量较高的变质玻璃进入料盆,就会使产品产生条纹。料道中玻璃液的温度越低,料滴重量越大,产生条纹的几率越大。电熔锆刚玉砖中部也不是不被侵蚀,只是相对说来要轻微一些。
除此之外,窑炉和工作池与玻璃液接触的电熔锆刚玉砖被腐蚀后,也有一部分沉积于窑炉底部。特别是熔化部,由于温度高,而且与配合料接触,池壁砖的侵蚀腐蚀十分强烈,3~4年池壁砖厚度就腐蚀掉约2/3(初期侵蚀腐蚀快,后期由于冷却的原因,侵蚀腐蚀物粘度大,附着在池壁砖上流动得缓慢,因而侵蚀腐蚀速度较慢一些),由于腐蚀物粘度大,体积密度大,因而绝大部分沉积于窑炉底部。随着这种腐蚀物的富集累积,或池底温度变化,这层变质玻璃也会随着玻璃液流,进入到供料道中,造成产品条纹。
由于电熔锆刚玉料槽砖表面腐蚀物是顺着料槽底部流动的,所以一般的搅拌方法是解决不了的,因为搅拌器很难作用到料道底部,不可能充分搅动料道底部的玻璃液[2]。如何鉴别这种条纹呢?如果同一组机器或同一工号的产品,其条纹所在部位和形状都一样,匀料筒左转、右转都解决不了,就是这种由于电熔锆刚玉砖被腐蚀所产生的条纹。
国外发明了一种供料道底部泄料装置,它在供料道底部有一道槽沟,槽沟中央有一个泄料孔,见图一,或在供料道底部有一道弧形装置,弧形装置顶端有一个泄料孔见图二。不管是图一还是图二中的料槽砖,其内侧底角不要形成直角,最好是弧形斜面。这样可以去除死角,使料道底部的脏玻璃移至放料点[3]。变质或被腐蚀物污染的玻璃流进料盆之前,先进入这道槽沟里从泄料孔底部排泄掉,从而有效解决因侵蚀物进入料盆而产生的条纹。其详细机理,请参照华东理工大学博士生导师孙承绪教授写的“料道电加热放料机构”一文。
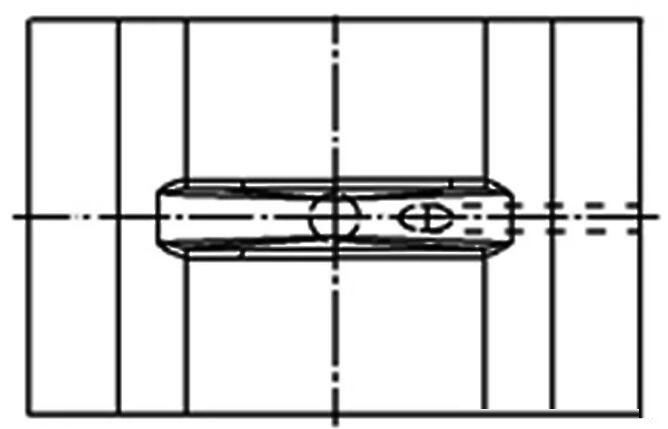
图 1
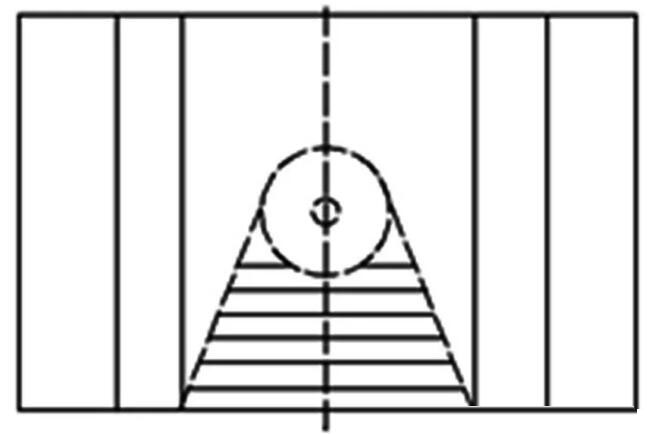
图 2
有人认为这种条纹是工作池、料道温度不均造成的,试想在直径30~50mm的玻璃料滴上,条纹只有几十丝或1mm左右,它们的温度会差几十上百度吗?它们的表面张力、粘度差别会如此之大吗?显然不可能。料滴温度不均只会产生厚薄不均,即便产生条纹也是较宽的板状条纹(其实质也还是玻璃成份不均质造成的)。
该供料道泄料装置为电加热装置,它由两根电极或一个电加热筒来控制该处玻璃液温度,若发现条纹,将控制柜上的电源开关打开,然后通过可控硅控制电流大小,从而控制温度高低,很快就达到玻璃液软化流动温度,底部就开始泄料。若没有条纹时,电源开关关闭,泄料孔的玻璃液就逐渐冷却,不再流动,操作十分简便,不影响生产。
该供料道泄料装置完全可以取代搅拌装置,电熔锆刚玉搅拌浆每5~6个月要换一次,换时要缓慢烘烤,以防炸裂。烧结材料做的搅拌浆,虽然热稳定性好一些,但抗磨损侵蚀性能差一些,一般3个月换一次。搅拌浆刚放入供料道时在玻璃液中要产生气泡,从而影响生产。另外搅拌浆被磨损腐蚀下来的物质也还是进入玻璃液中了,只是量少被搅散了,不易被发现而已。而泄料装置安装上去,使用方便,发现产品条纹,通电就可泄料,不用时将电源关掉即可,基本上可以用一个窑期,中途仅换泄料电极板就行了,方便快捷,不影响生产,综合成本要比搅拌装置低,效益要好得多。
下面就传统搅拌和供料道泄料做成本比较:
传统搅拌装置
1、机械传动装置(双搅拌):40000.00元
2、搅拌浆(按电熔AZS,一年换两次)材料费:10000.00元/年
3、换搅拌浆影响生产:按6组单滴行列机算,每次影响5小时,为14040只瓶子,一年换两次,少收28080只瓶子,每只单价平均为1.8元(高白料酒瓶),其产值为:50544. 00元。
4、另有占总产量5%因搅拌浆解决不了的条纹所造成产品减产,其数量为(按6组单滴行列机,每年按330天计算)926640只/年,产值为1667952.00元。
供料道泄料只是一次性投资,中途维护对生产没有影响,直接效益是十分可观的,再加上对产品质量提升所产生的间接效益,使用泄料装置的优势就显得十分明显。